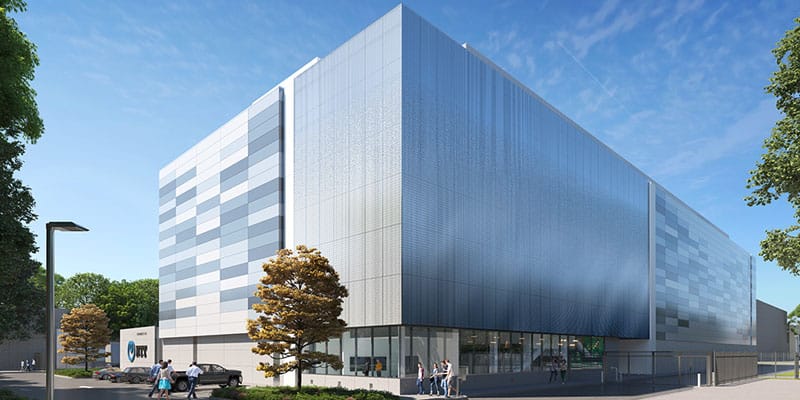
How Vibration Control in Data Centers Can Protect Our Modern Lives
Vibration Isolation Systems are used on the Mobile Launch Platform to mitigate vibrations from the launch and protect important electronic equipment from damage.
Vibration Isolation Systems are used on the Mobile Launch Platform to mitigate vibrations from the launch and protect important electronic equipment from damage.
Vibration Isolation Systems are used on the Mobile Launch Platform to mitigate vibrations from the launch and protect important electronic equipment from damage.
Application of Taylor Devices dampers in a steel frame structure building.
The two frame office towers, constructed in the 1970s per the 1967 edition of the UBC, use perimeter reinforced concrete moment frames to resist seismic loading. The buildings are rectangular in plan and have certain characteristics that adversely affect their seismic performance, in particular the presence of a soft-story response at the first floor (approximately 50% taller than typical floors), and limited ductility typical of buildings of that era. Risk analysis showed that for the towers the PML exceeded 20%. Nonlinear response history analysis (NLRHA) of the towers was conducted and showed that in the existing configuration, the story drift ratios (SDRs) at the first floor exceeded 2%, shear hinging of the first floor beams was expected and that the SDRs would need to be reduced to approximately 1.4% for the first floor to limit the extent of nonlinear response. Seismic retrofit included addition of 300-kip viscous dampers in both directions to the first floor of the building.
A roof isolation system is proposed as a means to reduce the detrimental effect of earthquakes in buildings. This roof isolation system entails the insertion of flexible laminated rubber bearings between a building’s roof and the columns that support it and the addition of viscous dampers connected between the roof and the rest of the building. The properties and dimensions of the rubber bearings and viscous dampers are selected in a way that makes the roof, bearings, and dampers form a highly damped vibration absorber. Presented also is a comparative study with a simple five story steel building under a strong earthquake ground motion that is carried out to assess the effectiveness of the proposed system. In this comparative study, it is found that the roof isolation scheme reduces the floor displacements and interstory drifts of the analyzed building by as much as 83 percent. On the basis of these results and in view of its simplicity, it is concluded that the proposed roof isolation system has the potential to become a practical and effective way to reduce earthquake damage in buildings.
This paper provides a literature review on the application of base isolation and supplemental damping systems for seismic protection of wood structures. The review reveals that both elastomeric bearings and sliding bearings have been considered for implementation within base isolation systems of wood framed buildings. In addition, friction dampers, viscoelastic dampers, hysteretic dampers, and fluid viscous dampers have been considered for implementation within the framing of wood buildings. Although there are a number of impediments to the widespread implementation of such advanced seismic protection systems, the reviewed literature clearly demonstrates that advanced seismic protection systems offer promise for enabling light framed wood structures to resist major earthquakes with minimal damage.
This article appeared in Special Operations Technology magazine. It provides a very complete explanation of the Taylor Devices isolated seat for the Navy, complete with many photos. The article also includes the experiences of the seat occupants under high speed ocean travel.
This paper summarizes a feasibility study for implementing seismic protective systems into high tech industrial structures in which costly vibration sensitive facilities are housed. Micro-vibration control of an IC fab is essential for optimum yield of reliable chip products. This paper describes the micro vibration analysis and measurement of a test structure before and after the incorporation of Seismic Protective systems. Based on the study, it is found that the incorporation of viscous dampers both enhances seismic safety and also minimizes the micro vibration of the structure. Viscous damper seismic isolation is the most promising method to achieve the “fully operational” seismic performance level of an IC fab.
This paper describes the dynamic analysis of an isolator system for the cabinet-mounted low voltage power switchgear in the Space Shuttle Mobile Launch Platform (MLP). The addition of electronic sensing and control components to this cabinet combined with the harsh vibration environment experienced during a Shuttle launch necessitated a six degree of freedom isolation system to prevent the spurious tripping of breakers. An added benefit of the isolation system is that it provides vibration isolation during the Shuttle’s approximately three mile journey between the Vehicle Assembly Building (VAB) and either of its two launch pads. The isolation system was designed, built, and integrated within the MLP. Broadband dynamic measurements were made during an actual Shuttle launch to verify the effectiveness of the isolation system and to validate the predictions of the analysis. Measurements made during the launch of STS-115 on September 9, 2006, affirmed the effectiveness of the isolators and validated the predicted performance of the isolation system.
The spring-damper isolators described in this paper were used on the world’s largest cable stayed bridge – the Sutong Bridge over China’s Yangtze River, completed in 2008. The Sutong Bridge is located north of Shanghai in China’s Jiangsu Province at a site where catastrophic earthquakes, typhoons, and ship impact are key design issues. The total length of the bridge is 4.7 miles, with a .67 mile long center span. The tall support towers of this bridge and the long support cables create long period motions along the primary axis of the bridge. The need to accommodate thermal expansion and contraction of the deck axially means that extensive motion can occur in this direction. The configuration of the bridge permits large axial motion of the suspended deck during earthquakes, typhoons, and synchronized truck/car braking loads such as would occur during a mass vehicular accident on the bridge. During dynamic earthquake loading, the long period of the suspended deck provides inherent isolation, albeit essentially undamped. Analysis indicated that added viscous damping would reduce deck motions substantially. During other events like typhoons and vehicle loading, analysis determined that the most cost-effective solution was to incorporate a snubbing type spring element that would only engage (become active) when the damper was approaching its end of travel in either extension or compression. The spring-dampers on this bridge have only damping forces for roughly 85% of the available displacement from the neutral (center of travel) position. Beyond this travel the spring element engage and a combined response of spring plus damper forces results. Essentially, the spring elements are “gapped” through all but approximately the last 15% of the damper stroke in either direction.